Bandbehandlungsanlagen müssen ein breites Produktspektrum bearbeiten, zu dem auch moderne hochfeste Stahlgüten gehören. Die teilweise schwer schweißbaren Materialien müssen im Einlaufbereich einer Bandanlage in kurzer Zeit sicher verbunden werden.
Speziell geeignet für Modernisierungen
Bereits bei der Entwicklung der Maschine wurde besonders Wert auf eine kompakte Bauweise mit einfachen Anforderungen an das Fundament gelegt. Die Kernmaschine benötigt nur einen Bauraum von 3,5 mal 4,0 mal 7,5 Metern, so dass sich eine Einplanung in ein vorhandenes Linienlayout auch bei schwierigen Platzbedingungen realisieren lässt. Somit eignet sich die Maschine nicht nur für die Integration in neue Bandbehandlungsanlagen, sondern auch perfekt für Modernisierungen und den Ersatz älterer Schweißmaschinentechnologien.
Zum Beispiel entschied sich SSAB Europe bei der Modernisierung seiner Beizlinie in Hämeenlinna in Finnland für den X-Roll® Laser Welder. Trotz des anspruchsvollen Produktspektrums konnte hier eine schnelle Inbetriebnahme und Hochlaufkurve erreicht werden. Bei einem weiteren europäischen Kunden wird die Maschine aktuell in den Einlaufteil einer Konti-Kaltwalzlinie integriert.
In der modernisierten Beizlinie von SSAB verbindet der X-Roll® Laser Welder Stahlbänder mit Dicken von 1,5 bis 6,5 Millimetern und Breiten zwischen 650 und 1.650 Millimetern. Die Schweißmaschine im Werk Hämeenlinna in Finnland ist mit einem Festkörperlaser ausgestattet. SSAB entschied sich für den X-Roll® Laser Welder, da die Maschine das Schweißen von hochlegierten Stahlgüten mit gleichzeitig niedrigen Zykluszeiten ermöglicht. Nach Beendigung der Umbauphase Ende 2018 konnte SSAB sein Produktspektrum erweitern und es können nun auch moderne hochfeste Stahlgüten problemlos verbunden und in der Linie im kontinuierlichen Prozess bei hohen Geschwindigkeiten gebeizt werden
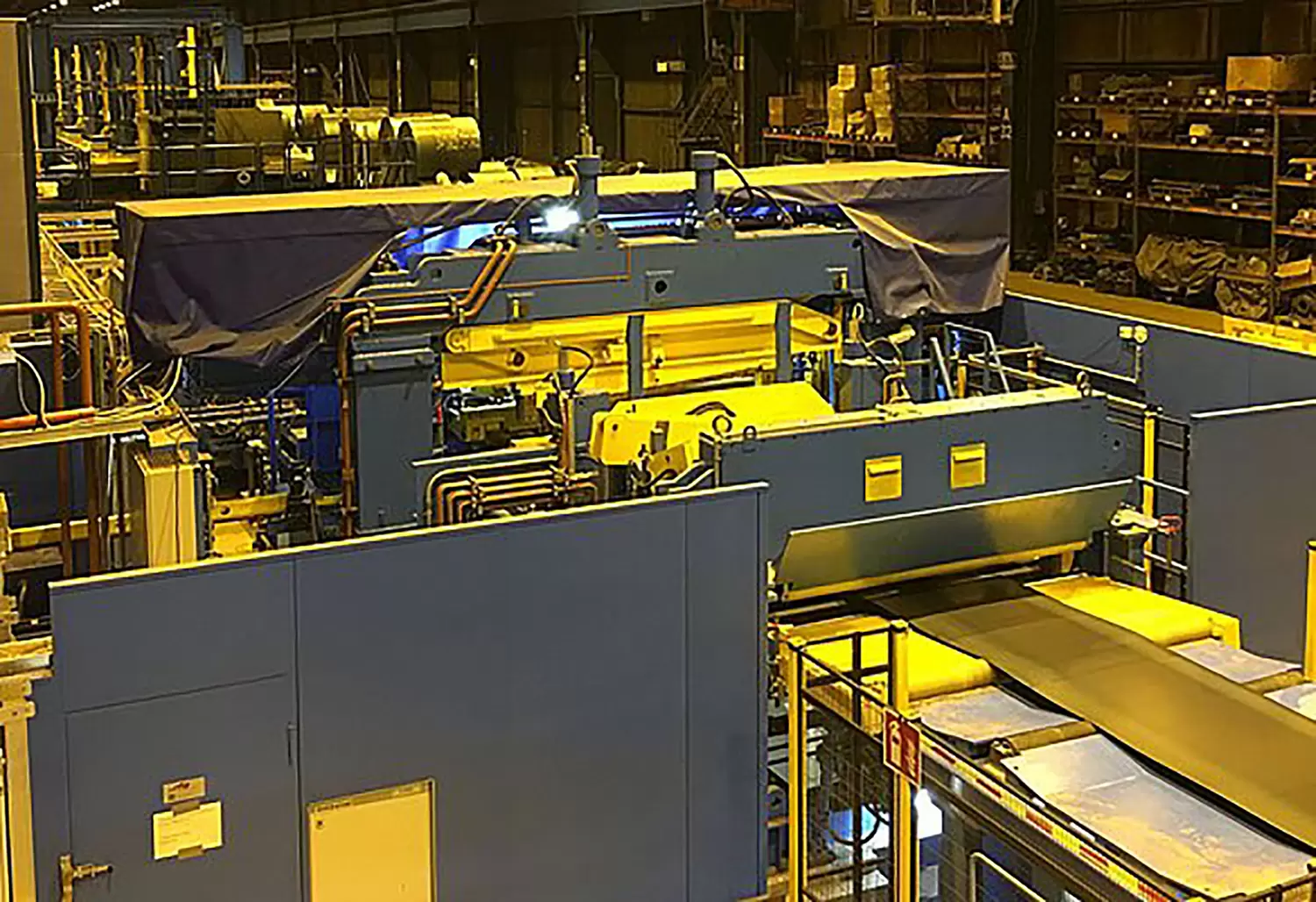
Patentierte induktive Wärmebehandlung der Schweißnaht und Qualitätssicherungssystem
Ein wesentlicher Vorteil der Maschine ist die patentierte induktive Vor- und Nachbehandlung der Schweißnaht, wodurch ein individueller Wärmebehandlungsprozess ermöglicht wird. Da jede Materialkombination individuelle Ansprüche aufweist und die Palette der möglichen Materialkombinationen deutlich zugenommen hat, sind die Abstände und somit der Zeitpunkt sowie die angewendete Leistung der induktiven Einheiten variabel. Das heißt, Behandlungszeit und Temperatur werden flexibel für jede Materialkombination eingestellt. Die hocheffiziente Tiefenwärmebehandlung mittels Mittelfrequenzinduktion ermöglicht eine Durchwärmung des Materials in kürzester Zeit und verhindert so einen Härteanstieg an der Schweißnaht und die damit verbundene Gefahr eines Bandrisses. Das spezielle Induktor-Design reduziert die Haltezeit im Vergleich zu herkömmlichen Systemen erheblich. Dies ermöglicht das Schweißen von schwer schweißbaren Materialien wie martensitischen sowie kohlenstoff- oder siliziumreichen Typen.
Das integrierte automatisierte Schweißnaht-Qualitätssicherungssystem bewertet den gesamten Schweißprozess. Über ein userfreundliches Interface bekommt der Bediener eine Indikation über den gesamten Prozess. Es werden verschiedenste Parameter der Schweißnaht überprüft, wie beispielsweise die Geometrie oder die Temperatur, und gehen in die Gesamtqualitätsbewertung der Schweißnaht ein.
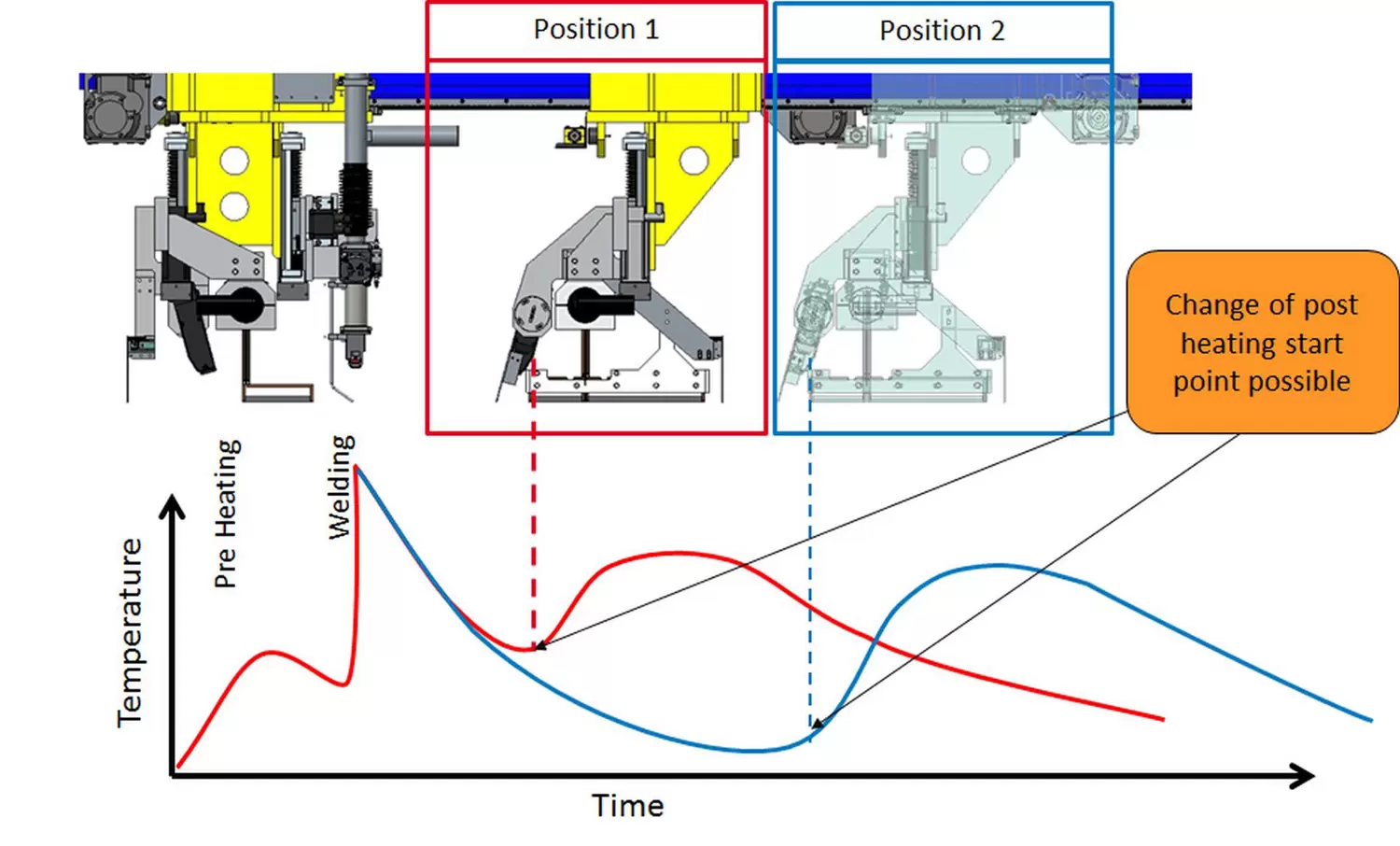
Automatische Kalkulation der Schweißparameter
Die Schweißparameter werden durch die automatische Kalkulation anhand der chemischen Analyse der Stahlschmelze individuell auf jede Materialkombination angepasst. Dank dieser automatischen Berechnung werden auch Kombinationen unbekannter Stahlsorten direkt erfolgreich verschweißt. Für die Berechnung sind lediglich die geometrischen Banddaten und die Analyse der Stahlschmelze der beiden Stahlbänder erforderlich.
90 percent of the operating expenses can be saved as compared to conventional machines with carbondioxide laser source thanks to high efficiency as well as lower running and maintenance costs.
Komponenten für hohe Produktivität und einfache Wartung
Niedrige Zykluszeit ermöglicht niedrige Nebenzeiten
Eine weitere Eigenschaft der Maschine ist ihre deutlich verringerte Zykluszeit. Durch das intelligente Maschinendesign sind alle Sequenzen im Schweißzyklus optimiert und führen zu deutlich kürzeren Gesamtzykluszeiten als bisher auf dem Markt üblich. Die kurze Zykluszeit der Schweißmaschine ermöglicht, die Einlaufnebenzeiten der Linien zu senken, wodurch indirekt die Produktion erhöht werden kann. Ein Austausch der bestehenden Schweißmaschine führt also nicht nur zu einer Erweiterung des Produktspektrums.
Schneller Wechsel der Messerkassetten
Auch die Austauschzeit für obere und untere Messerkassetten in der Schere ist durch ein spezielles System extrem kurz. Beide können in weniger als 30 Minuten gewechselt werden. Dies ist das Ergebnis eines „intelligenten Maschinendesigns“ ohne zusätzliche Ausrüstung, die in der Maschine benötigt wird, um diesen schnellen Wechselvorgang zu ermöglichen.

Frei wählbare Schweißquelle
Dank des modularen Aufbaus der Schweißmaschine und der damit verbundenen Trennung zwischen Schweißnahtvorbereitung und Schweißprozess kann die Schweißquelle einfach ausgetauscht werden. Somit ist es möglich, sowohl eine konventionelle CO2-Laserquelle einzusetzen als auch eine moderne Festkörperlaserquelle. Der hohe Wirkungsgrad, die geringeren Betriebskosten und die geringen Wartungskosten senken die Betriebsausgaben um bis zu 90 Prozent gegenüber konventionellen Maschinen mit CO2- Laserquelle.
Digitalisierung
Mehrere digitale Lösungen sind in dieser Maschine implementiert, um den Produktionsprozess möglichst simpel zu gestalten. Alle relevanten Prozessdaten werden in einem Archiv gespeichert und können zur Erstellung eines Wartungsplans genutzt werden. Die Dokumentation der Maschine ist digital verfügbar und verknüpft mit den verschiedenen Anwendungen. Zusätzlich bietet die SMS group einen Remote Service an, mit dem innerhalb kürzester Zeit auf Probleme des Kunden reagiert werden kann. Hierbei hat ein Mitarbeiter die Möglichkeit, sich virtuell auf die Kundenmaschine aufzuschalten und eine erste Problemanalyse durchzuführen.
Wesentliche technische Daten der X-Roll®-Laserschweißmaschine für Warmband
Material | Kohlenstoff, Edelstahl, Siliziumstahl |
Banddicke | 1,0 bis 6,5 mm |
Bandbreite | 650 bis 1.950 mm |
Größe der Kernmaschine | 3,5 m (Breite) x 4,0 m (Höhe) x 7,5 m (Tiefe) |
Gewicht der Kernmaschine | 65 t |
Laserquelle | CO2 / Festkörperlaser |
Weitere Informationen
Sie wollen noch mehr über unsere X-Roll® Laserschweißmaschine erfahren. Melden Sie sich bei SMS group #Connect an, dort finden Sie einen Fachbericht.
Strip processing lines have to treat a wide product range including state-of-the-art high-strength steel grades. Although some of the materials are difficult to weld, they must properly be joined in the entrysection of a strip processing line within a short period of time.
The X-Roll® laser welder offered by SMS group has been specifically developed to meet the requirements involved in joining hard-to-weld strip material. One of the components developed to master this challenge is a patented, inductive heat treatment system. Further advantages are an automatic welding parameter calculation system, a quality assurance system, short cycle times and an exchangeable laser source. The laser welder has been installed in numerous new plants, but also as part of modernization projects.
The X-Roll® laser welder offered by SMS group has been specifically developed to meet the requirements involved in joining hard-to-weld strip material. One of the components developed master this challenge is a patented, inductive heat treatment system. Further advantages are an automatic welding parameter calculation system, a quality assurance system, short cycle times and an exchangeable laser source. The laser welder has been installed in numerous new plants, but also as part of modernization projects. For the revamp of its pickling line in Hämeenlinna, Finland, SSAB Europe decided in favor of an X-Roll® laser welder. Despite the demanding product portfolio, commissioning could be done within a short time followed by a steep ramp-up curve. At present, a further machine is
being installed in the entry section of a continuous cold rolling mill at another European customer.