Mr Dahmen, let’s start with the news: SMS group has just signed a contract with H2 Green Steel in Sweden about the supply of a new greenfield steel mill. What is so unique about this project?
Burkhard Dahmen: H2 Green Steel will build the first carbon-neutral steel plant in the world. We supply the entire process equipment from ironmaking to the finished products. The direct reduction plant will be the first commercial facility in the world operating 100 percent with hydrogen. H2 Green Steel will reduce CO₂ emissions by up to 95 percent compared to traditional steelmaking because fossil fuels like coal or natural gas are almost completely dispensed along the entire process chain. This project shows the carbon-neutral future of steelmaking, and we prove that this is possible on an industrial scale – by the mid of this decade already!
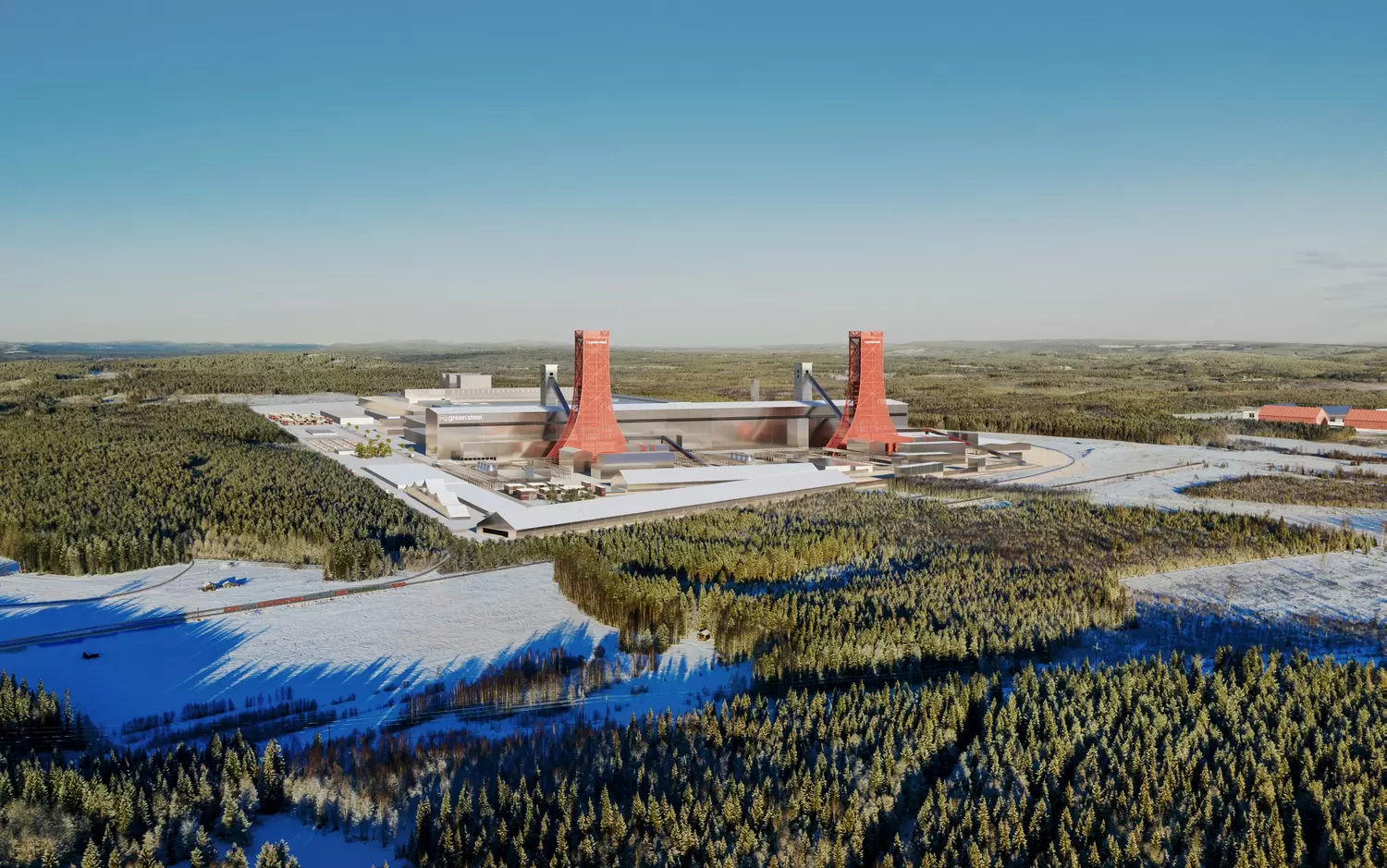
Does this mean the steel industry can quickly do its part to achieve climate neutrality?
Burkhard Dahmen: Yes and no. It is true, the solutions to fully decarbonize the steel industry are at hand. But greenfield projects like H2 Green Steel are an exception right now. Most of our customers are starting by modernizing their existing plants. With our solutions, large-scale quick wins are possible here. We can reduce the carbon footprint of an existing blast furnace by around 30 percent, mainly by injecting hydrogen or hot synthesis gases.
Our metallurgy team in Luxembourg is currently working on a new furnace that achieves a CO2 savings potential of up to 70 percent. In combination with carbon capture, this could result in climate neutrality. If everything goes as planned, this technology will significantly contribute to the decarbonization of existing steel mills.
Of course, ironmaking is a focus of both SMS and our customers because 80 percent of greenhouse gas emissions come from the primary production stage. But we also have solutions for the downstream processes from steelmaking to the finished product. Take our digital solutions like the Viridis energy platform: This is a comprehensive energy management solution that improves the energy performance along the entire value chain while reducing energy-related expenses, raw material consumption, and finally, carbon, greenhouse gas, and waste emissions.
We're taking a leading role in the transformation of our industry. Let’s turn metals green to save the earth’s climate.
So, SMS group really seems to have accepted the challenge for a sustainable metals industry, right?
Burkhard Dahmen: Yes, our mission is “turning metals green”. We’re taking a leading role in this transformation. That’s because we’re uniquely positioned to do so in several ways. First and foremost, we develop the solutions that our customers, the steel producers, for example, need to do their job well – producing the metals society needs, but with minimum environmental impact. The steelmakers can only be as good as the solutions we create for them – they count on us for that. It means we have a big responsibility here.
Our history has brought us to this point – 150 years of relentless pursuit of process expertise and building a network of companies, within and outside of SMS group, that are uniquely qualified to tackle the industry’s transformation. No other company can bring all of the most relevant climate-neutral processes to the table. We do that on two levels: On the decarbonization front, we can turn metals production carbon-neutral, based on green electrical power and green hydrogen. And we play a significant role in what’s called circular economy – developing and optimizing technologies for bringing valuable metals back into circulation.
Recycling metals is nothing new. What does progress look like there?
Burkhard Dahmen: You are right. Everybody knows that metals are perfect for a circular economy. Take aluminum, for example: Recycling it can lower the CO2 footprint by more than 90 percent compared to primary production. Our goal is to push the boundaries of recycling rates to their technological limits – for steel, for aluminum, and especially for copper and all other non-ferrous metals which have become increasingly important.
But that’s by no means the only benefit. Recycling is a significant factor in saving the earth’s resources and makes us less dependent on what’s still in the ground – it’s also often an ethically sound alternative and reduces the dependency of countries without access to primary raw materials.
Now, recycling major metals is a well-established process worldwide, but we’re also putting all our metallurgical know-how to use for bringing additional metals back into the circle. One crucial area in which we’re making that happen is batteries. For example, we formed the joint venture Primobius to market recycling technology for recovering lithium, nickel, cobalt, and other materials from consumer electronics as well as lithium-ion batteries from electric vehicles. In doing so, we lay the foundation for bringing high-purity raw materials back into use.
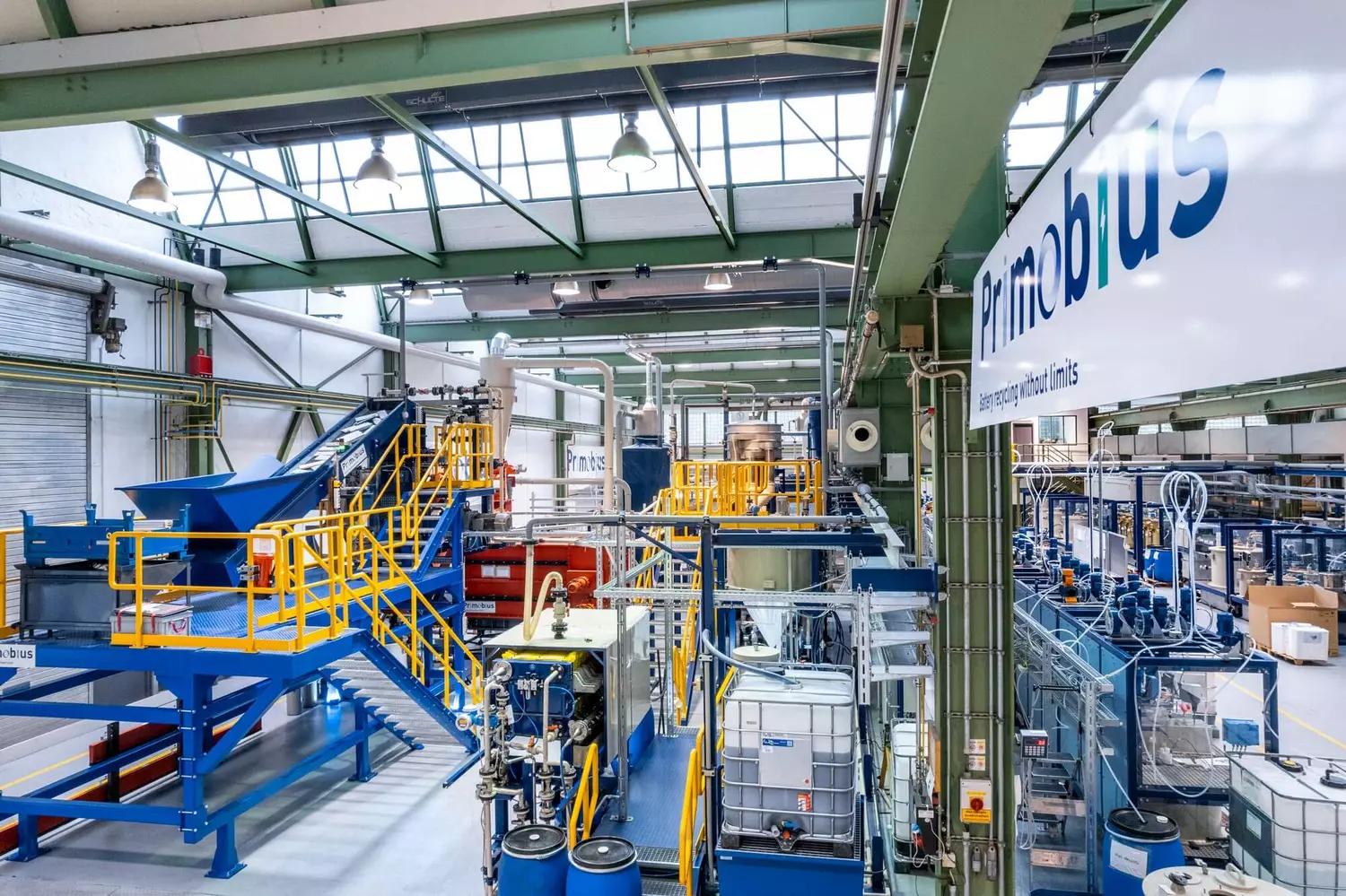
So what’s the outlook for SMS group and plant engineering companies like you?
Burkhard Dahmen: We’re all going to be very busy for many years – transforming the metals industry will take more than a generation. Some basic arithmetic makes that very obvious: In order to meet international climate goals by 2050, about 35 million tons of crude steel capacity must “go green” every year. That translates into around nine traditional integrated steel mills which will have to be replaced with their modern equivalent every year! These days, we’re putting a lot of resources into gearing up our capacity to meet that demand. That includes people, of course. I can only say, for purpose-driven individuals on a sustainability mission, plant engineering is the place to be. Let’s turn metals green to save the earth’s climate.