Our customer decided to push product quality at the CSP® plant and explicitly wanted to improve product quality KPIs by reducing longitudinal facial cracks. At the same time, higher productivity and a more secure plant operation was to be assured by avoiding breakouts.
The customer was facing an unwanted high rate of breakouts per quarter. SMS group was asked to investigate and provide a path to resolution. Understanding how different factors were contributing to longitudinal facial cracks and breakouts, detecting the defects was not a sufficient solution as once cracks were detected, breakouts were not far behind. A predictive solution that provides actionable operator support was needed in this case. The perfect match for our Cracks Preventer, a combination of artificial intelligence and SMS group`s unique domain knowhow. The product focuses on preventing the defects so that they can prevent the breakout from happening instead of only detecting the defect after it occurs.
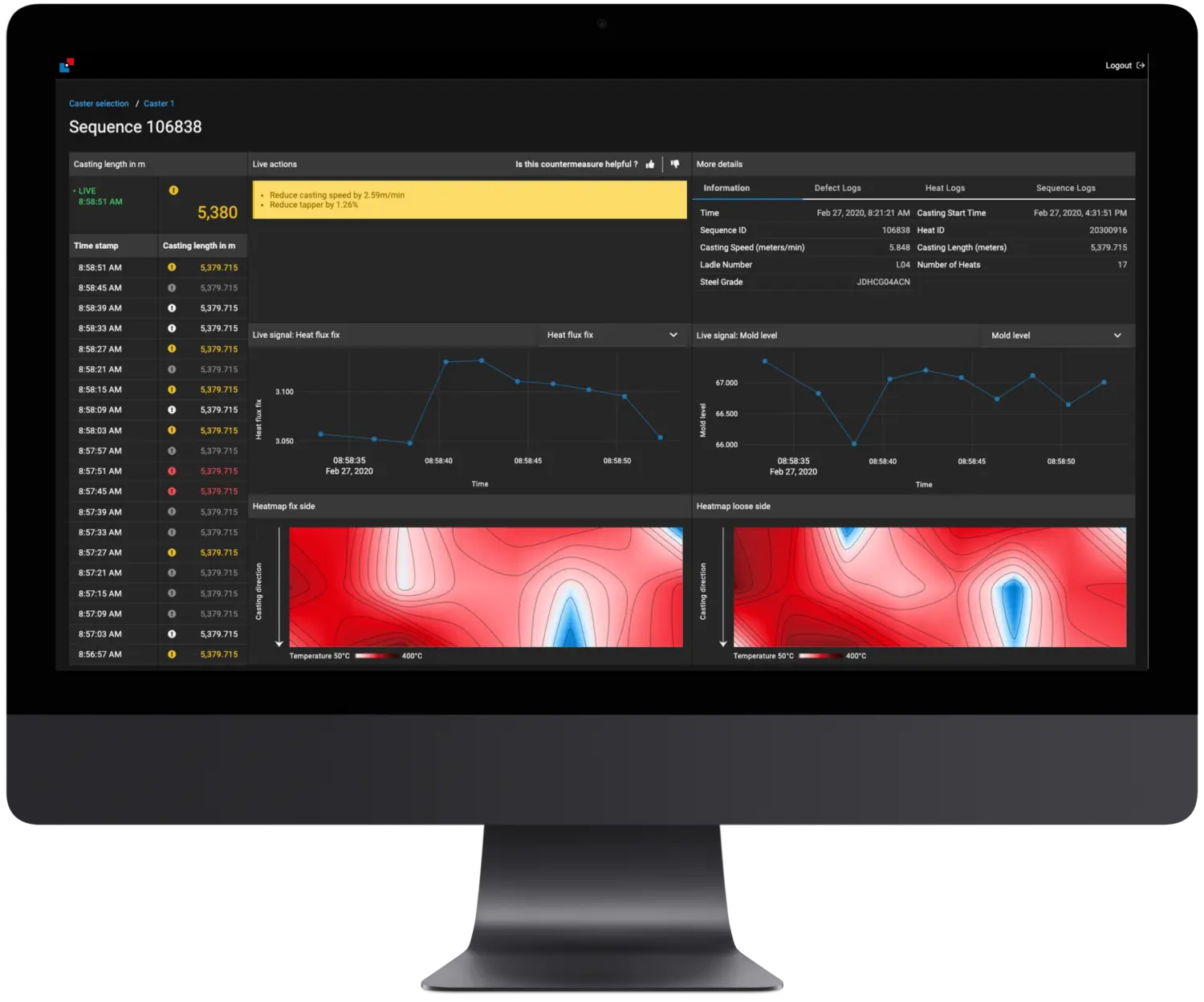
Metallurgical knowhow meets AI expertise
Fortunately, a sufficient amount of data was available for us to implement an AI-based solution that could address the problem. Cracks Preventer resolves quality issues in casting processes by merging SMS group`s unique domain knowhow with artificial intelligence methods. It prevents downgrading caused by multiple surface defects, like corner cracks, slivers or lamination. To do so, Cracks Preventer learns from historical process data and investigates all relevant process data in real-time. That way defects can be detected before they occur. In this case, we obtained additional real-time data from the customers IBA system, as well as post-process slab data and optical inspection data from their Parsytec system.
Based on the analysis results, Cracks Preventer can predict what is to be done. It presents countermeasures to the operator which then can be implemented into the level 2 process control right away. Thus Cracks Preventer not only avoids downgrading it also helps to smoothen casting processes. Both aspects are of high importance for successively creating a more sustainable metals industry.
Prime Optimizer
In a next development stage Cracks Preventer can be enabled to feedback adapted set-points based on real-time production data into the automation system. That way the necessity for human intervention is reduced even further and product quality in casting processes is improved.
Cracks Preventer is a real-time crack prevention solution with an easily customizable customer front-end and real-time actionable items for the operator. It sends heat and sequence-level suggestions to the respective department to improve the process in long term. It is tied into a closed control loop with the existing plant automation systems.
Software-as-a-Service
Cracks Preventer is characterized by a high degree of flexibility for its users. This enables a wide range of services that can be tailored to the customer. The customer has the freedom to choose between pre-customized software package or a tailormade solution that helps tackling indiviual use cases or defect types.
Together with our customer we develop a business model based on the desired setup. Starting from regular software licensing over software-as-a-service to performance-based models. Bundling all of SMS groups' competences with regard to equipment and process automation, the highly flexible technology of Cracks Preventer and our dense service network, we can build holistic quality improvement solutions for continuous casting, that include not only software but also on-site service, spare part management, or off-line services like maintenance for caster segments for instance. According to the desired solution a business model is designed that meets individual customer needs.